鑄鋁件的補(bǔ)縮和澆鑄工藝:補(bǔ)縮和澆鑄的過程包含了所有要采取的措施,來確保適當(dāng)?shù)哪P蜐沧ⅲǔ掷m(xù)的固化和在固相前沿加入新的液相金屬。這其中包括澆注口,流道和內(nèi)澆道的正確的成形,尺寸和位置,而這些考慮 產(chǎn)品的實(shí)際需要,例如分離半型,從澆注口和澆流道以及將鑄件取出來,并后將流道敲掉。澆注口和澆流道所需要的金屬的量決定了出成率,而因此對成本有很大的影響。出成率依賴著鑄品的形狀,依賴模具的制造過程和鑄造過程的本身。這影響的程度達(dá)到40%-90%。出成率50%意味著用于澆注鑄品的液相金屬的量是 已計(jì)劃鑄件成分中金屬量的兩倍。砂模鑄造通常比模具鑄造出成率低。頂端填料和等價(jià)的方法比如低壓模鑄,這些方法實(shí)際上是 沒有澆注系統(tǒng)的空腔澆注,比底端填料的出成率好,然而頂端填料的方法需要在的條件下進(jìn)行,因?yàn)樗赡芤鹧趸锏漠a(chǎn)生和誘導(dǎo)作用。澆道的設(shè)計(jì)通常只考慮 模具填料,意思是 澆道的設(shè)計(jì)確保當(dāng)考慮 到適當(dāng)?shù)慕禍貢r(shí)有正確的塑變,流速和壓力。現(xiàn)在計(jì)算塑變參數(shù)時(shí)已經(jīng)有了程度的改進(jìn),因此可以適當(dāng)?shù)脑O(shè)計(jì)系統(tǒng)。一個(gè)進(jìn)一步的邊界條件是 避免發(fā)泡的需要,因?yàn)殇X的密度低并且容易被氧化。這導(dǎo)致了對大流速的限制,需盡大可能保持層件間塑變條件并避免超壓。在這種方式下氧化皮保持完好,并且澆鑄通過未被破壞的氧化皮形成的膠管來進(jìn)行。補(bǔ)縮的過程適當(dāng)?shù)难a(bǔ)償固化過程的收縮并且避免空位、氣孔和裂縫的形成。在固相凝結(jié)前沿持續(xù)的加入液相金屬。這是 指在漸漸固化的任何時(shí)刻都確保有一條從內(nèi)澆口到固相前沿的液相金屬的自由通道。定向凝固鑄件中大可能面臨填料不足的區(qū)域可以通過電腦模擬的固化過程很好的分析出來。補(bǔ)縮和澆鑄系統(tǒng)的設(shè)計(jì)因素要考慮 ,它們 嚴(yán)重影響出成率,盡管有特殊的絕緣體作為加熱襯墊。它們 需要和其他裝置一起很好的排列來幫助控制冷卻系統(tǒng)和一個(gè)正確的澆鑄溫度來確保定向冷卻和固化,所以即使在模具澆鑄過程中固相前沿一直適當(dāng)?shù)奶钊胄迈r的液相金屬。冷凍澆鑄特別適合這種方法。澆注口和開門系統(tǒng)的一些因素也影響到填料。
鋁鑄件縮松的產(chǎn)生原因及防止方法
現(xiàn)象:
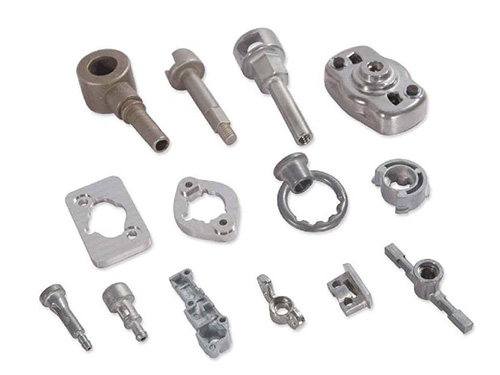
鋁鑄件縮松一般產(chǎn)生在內(nèi)澆道附近非 冒口根部厚大部位,壁的厚薄轉(zhuǎn)接處和具有大平面的薄壁處。在鑄態(tài)時(shí)斷口為灰色,淺黃色經(jīng)熱處理后為灰白淺黃或灰黑色在x光底片上呈云霧狀嚴(yán)重的呈絲狀縮松,可通過X射線、熒光低倍斷口等檢查方法發(fā)現(xiàn)。
產(chǎn)生原因:
(1)冒口補(bǔ)縮作用差。
(2)爐料含氣量太多。
(3)內(nèi)澆道附近過熱。
(4)砂型水分過多,砂芯未烘干。
(5)合金晶粒粗大。
(6)鑄件在鑄型中的位置不當(dāng)。
(7)澆注溫度過高,澆注速度太快。
防止方法:
(1)從冒口補(bǔ)澆金屬液,改進(jìn)冒口設(shè)計(jì)。
(2)爐料應(yīng)清潔無腐蝕。
(3)鑄件縮松處設(shè)置冒口,安放冷鐵或冷鐵與冒口聯(lián)用。
(4)控制型砂水分和砂芯干燥。
(5)采取細(xì)化晶粒的措施。
(6)改進(jìn)鑄件在鑄型中的位置,降低澆注溫度和澆注速度。
簡述鋁鑄件的凝固方式
1、逐層凝固
純鋁或共晶成分鋁合金在凝固過程中不存在液、固并存的凝固區(qū),故斷面上外層的固體和內(nèi)層的液體由一條界線(凝固前沿)清楚分開。隨著溫度的下降,固體層不斷加厚,液體層不斷減少,直達(dá)鋁鑄件中心,這種凝固方式為逐層凝固。
2、糊狀凝固
如果鋁合金的結(jié)晶溫度范圍很寬,且鋁鑄件的溫度分布較為平坦,則在凝固的某段時(shí)間內(nèi),鑄件表面并不存在固體層,而液、固并存的凝固區(qū)貫穿整個(gè)斷面,類似于水泥凝固,糊狀而后固化,稱為糊狀凝固。
3、中間凝固
大多數(shù)凝固介于逐層與糊狀凝固之間,稱為中間凝固。一般來說,鋁鑄件質(zhì)量與其凝固方式密切相關(guān)金的充型能力強(qiáng),便于防止縮孔和縮松;糊狀凝固時(shí)是 獲得緊實(shí)的鋁鑄件的凝固方式。
壓鑄鋁件的澆鑄工藝:澆口和冒口的目的是 為了被償鋁合金在冷卻和固化階段的收縮,給鑄造的后部分的固化提供額外的液態(tài)金屬。不可能在鑄件所有的需要冒口的地方都提供冒口。適當(dāng)?shù)奶盍霞夹g(shù)將保證在定向固化的條件下后是 冒口凝固,這施加了以下的條件:保證澆、冒口一直有足夠的可以獲得的液態(tài)金屬;從澆口到鑄件需要填料的部分之間有一條液態(tài)金屬的通道,而且這條通道在鑄件固化以前保持是 可以通過的。如果需要填料的區(qū)域和冒口區(qū)域的固化之間有足夠大的時(shí)間差,就可以實(shí)現(xiàn)以下的條件,因?yàn)檫@樣當(dāng)需要填料的區(qū)域剛剛完成固化的時(shí)候,在冒口中還有液態(tài)金屬存在。這里應(yīng)用了特定的溫度梯子,通過定向固化來確定。
熔體制備:爐子和爐料的暴露的面積越小,熔體的損失就越小。燃料加熱爐的熔體損失要比電加熱爐高。因?yàn)榱鬟^它們 的氣體多。氧化物不利的影響著液態(tài)金屬的流動(dòng)性和金屬鑄件的力學(xué)性能,尤其是 剛玉和尖晶石內(nèi)的粗糙的內(nèi)含物。同時(shí)它們 降低了組件的承重能力,而使它難加工,因?yàn)檫@些內(nèi)含物要比金屬硬而易導(dǎo)致工具磨損。含有鎂和氧化鋅的合金要比含量有銅和硅的多,同時(shí),熔體中形成的或引入的氧化物可以生長。另一個(gè)影響熔體質(zhì)量從而影響鑄造組件的質(zhì)量的主要因素是 熔體中氫的溶解度。液態(tài)的鋁和鋁合金可以通過減少水蒸氣而吸收氫,這些水蒸氣主要來自氣氛中,爐料,腐蝕的產(chǎn)物,爐子或傳輸器的襯里,甚至來自模具本身,從碳?xì)浠衔锏姆?解中氫也可能進(jìn)到熔體中。氫以原子的形式溶解,當(dāng)它從液體中浮出時(shí)重新結(jié)合成分子。對于氣泡來說形成理想的邊界面是 非 常的,這就需要成核。氧化皮和其他非 金屬內(nèi)含量物了氣孔的形成,因?yàn)樗鼈?刺激成核也因此刺激了氫氣氣泡的的形成。即使擁有同樣地氫含量,干凈的熔體要比那些含量有很多內(nèi)含物的熔體形成的鑄件具有低的氣孔率。在劇烈成核的的熔體中,氣泡可以在很低的溫度下形成。這些導(dǎo)致氫氣集中的水分的主要來源是 爐料本身,爐子襯里,坩堝材料,工具,鹽,溶劑,以及大氣的環(huán)境。因?yàn)闇囟仍礁撸垠w暴露在大氣中或停留在爐子中的時(shí)間越長,氫的含量上升得越快,甚至達(dá)到飽和點(diǎn),所以鋁的熔體的溫度需要限制在750度以下。沒有的長時(shí)間的滯留需要避免。氫氣是 從表面被帶進(jìn)熔體中的,以一個(gè)由濃度梯度決定的受控的速度擴(kuò)散。
泊頭東固模具制造有限公司(http://www.hbdgmj.com)主營項(xiàng)目:壓鑄件流動(dòng)性好,易熔焊,釬焊和塑性加工,在大氣中耐腐蝕,殘廢料便于回收和重熔;但蠕變強(qiáng)度低,易發(fā)生自然時(shí)效引起尺寸變化。澆鑄鋁件零件加工變形的原因很多,與材質(zhì)、零件形狀、生產(chǎn)條件等都有關(guān)系。鋁件加工表面應(yīng)光潔、平正、鑄字標(biāo)志應(yīng)清晰,澆、冒口清理后與鑄件表面應(yīng)齊平。 汽車鋁配件對于邊蓋類薄壁零件,采用鈑金冷做校正;容易磨損的軸孔類零件可采用金屬噴鍍、焊修、膠粘、機(jī)械加工等工藝以達(dá)到原廠尺寸。